The development and manufacture of fuel cells require depositions of diverse coatings on several components of the fuel cell assembly such as the electrodes, electrolyte membranes, gas diffusion layers (GDLs), carbon paper layers, etc. There is a high demand for a precise method to apply thin, highly uniform, defect-free coatings of optimal thickness and texture. These are key attributes to achieving maximum load and high fuel cell efficiency at low manufacturing costs, critical to the production of PEM, DMFC and SOFC fuel cells.
The process presents many challenges with the application method and material handling.
Application method:
- The coating usually needs to be applied with precision in successive layers to achieve the optimal physical and electrical properties. This requires a spray pattern with uniform and stable shape and velocity.
- Traditional methods like air atomizing spray valves and nozzle-based spraying systems lead to clogging, regular maintenance and downtime.
- Coating pattern requires accurate positioning control and degrees of freedom.
- Ability to coat on substrates of different types and geometries:
- Nafion membrane
- Carbon paper
- Bi-polar/metal plates
- Ceramic plates and tubes.
Material handling:
- Capacity to spray various formulations:
- Metal oxide suspensions
- Carbon and precious metal-based (Pt, Ir, Ru, PtC) inks
- Ceramic slurries
- Copolymers and other proprietary formulations
- These mixtures and catalyst inks are expensive, requiring precision liquid delivery systems with accurate measuring and control capabilities to reduce material wastage and costs.
- Some suspension mixtures require regular stirring to maintain required physical properties during coating.
- Capacity to spray various formulations:

USI’s PRISM coating systems are ideally suited for the R&D and production of fuel cells. Featuring USI’s patented nozzle-less ultra-Thin Coating Application Technology (tCAT), PRISM systems deliver the thinnest, defect-free applications for the whole range of coating materials, offering the following advantages:
- Precise control of spray width: Two spray heads (CAT-ILDS Ultrasonic Head and Blade Ultrasonic Head) produce desired patterns of width 3 mm to 150 mm over various substrate geometries.
- Precise control of spray shape: An adjustable velocity air stream is used to expand and accelerate the ultrasonically-produced spray.
- Stable and uniform spray shape: Excellent coating uniformity and repeatability.
- Mixtures with high solids content: Flow rate and ultrasonic vibrations unaffected by the viscosity of mixture. Ability to spray fuel cell catalysts at up to 50% solids content.
- Avoids ‘fall out’ in suspensions: Lower frequency operation (35 kHz) ensures suspended particles remain entrained in droplets of uniform size and do not separate during atomization.
- No heating of liquid: Unlike a nozzle-based system, the nozzle-less spray design does not generate or impart heat to the liquid which might alter the mixture properties.
- Minimise waste of expensive catalysts: Very high transfer efficiency of about 95%.
- Substrate handling capabilities: Flexible membranes can be held in place during coating. Additional option for heated vacuum hotplate, rotational axis for tubular substrates.
Learn more on USI’s patented nozzle-less ultra-Thin Coating Application Technology (tCAT)
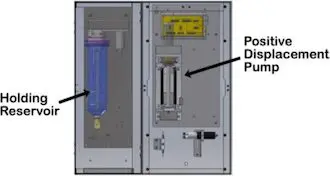
Precision Liquid Delivery System:
The coating liquid is fed to the liquid applicator with PRISM’s Precision Metering Pump (PMP), providing the following functions and benefits:
- Accurate control of liquid flow rate: Positive displacement metering pump with a micro-stepping drive to measure and control liquid flow.
- Instant ON/OFF activation of the spray: Controlled liquid delivery to atomizing surface resulting in significant reduction in overspray and improvement in precision.
- Integrated stirring mechanism: Syringe pumps with advanced design to ensure stirring to maintain consistent properties.
Programmable X-Y-Z positioning system:
- Accuracy in positioning: Coating applied to the substrate with an easily programmable spray head motion path.
- Programmed coating recipe: Successive coating layers applied with low cycle times.
- Fully automated repeatable process for high volume production
Product line for fuel cell coating processes:
- PRISM-400 BT (Benchtop): ideal for lab-scale applications
- PRISM-500: R&D and industrial applications
- PRISM-800: High-volume, high-throughput manufacturing
PRISM systems have been installed at multiple locations worldwide, serving diverse needs with unique, specialised configurations. NanoTechnology Solutions is the exclusive distributor of USI’s products in Australia and New Zealand. Contact us for support and additional information on production requirements.